Cracking of Welding Seams of Eccentric Reducers in Ultra-high Pressure Steam Pipelines
Posted: 06/16/2023 11:53:41 Hits: 35
Abstract: The cracking process of the welding seam of the reducer on the ultra-high pressure steam pipeline of the 220 kt/a ethylene plant of PetroChina Dushanzi Petrochemical Company was explained. Tests and other methods are used to find the cause of the cracking at the welding seam of the reducer to formulate maintenance measures for the ultra-high pressure steam pipeline, prolong the service life of the pipeline, and ensure the safety and economic benefits of the ethylene plant.
A super high-pressure steam ( SS ) pipeline is one of the most important pressure pipelines of an ethylene plant, and its long-term stable operation directly affects the output and benefit of an ethylene plant. The 220 kt/a ethylene cracking unit of Dushanzi Petrochemical Company of PetroChina was designed by the British SNAM Company and put into use in August 1995. The ultra-high-pressure steam pipeline was designed, installed and put into use at the same time. The ethylene unit has 7 cracking furnaces in total, and the ultra-high-pressure steam generated by each cracking furnace flows into the main pipe through the globe valve. On April 28, 2022, during the SS grid-connection operation of Furnace No. 4, cracks were found at the welding seam between the high-pressure steam main pipe of the cracking furnace and the tee. Since the device is in operation, the cracked part is repaired by welding after excavation, but it is impossible to take samples of the cracked part for physical and chemical analysis of the fracture. The reason for the cracking can only be determined according to the on-site inspection situation and historical failures.
1. Basic situation of ultra-high pressure steam pipelines
The eccentric reducing joint of the ultra-high pressure steam pipeline is made from A335-P22. The medium of the pipeline is ultra-high pressure steam, the operating temperature 525 ℃, and the operating pressure 12.5MPa. The size of the eccentric reducer is DN150 × DN250 mm; the wall thickness of the side of the small end is 23mm, and the large end 42 mm. On April 28, 2022, a leak was found at the reducer, and the ultra-high pressure is removed from the device immediately. The pressure of the SS system dropped to 1MPa, and the maintenance personnel removed the pipe insulation.
The welding seam at the small end of the pipe reducer is cracked. Judging from the size, opening and appearance of the crack, the crack extends downwards from the upper part along the fusion line. The crack length is about 240 mm. The fracture is flat from the outside. The welding seam was repaired and the cracking furnace was heated up. It is verified that the SS system was put into use in 1995 according to the operating conditions over the years. After inquiry, the number of shutdowns of the device for maintenance and the number of times pressure rise and fall of ultra-high pressure steam pipelines totaled 19 times.
2. Inspection status of ultra-high-pressure steam pipelines
Repairing the cracked parts by welding after excavation cannot be carried out. The complete observation and microscopic analysis of the fracture can only be carried out on-site for visual inspection, only analysis for alloys, on-site metallographic coatings, hardness and other tests can be performed.
2.1 Appearance inspection of reducers
The crack is located on the welding seam’s fusion line of the small end of the reducer of the SS pipeline. From the size and appearance of the crack opening, it is judged that the crack extends downward along the fusion line from the upper part, and the crack length is about 240mm. The short opening is flat viewed from the outside and has obvious characteristics of large stress cracking. There is obvious upward bending deformation at the bottom of the eccentric reducer (figure 1).
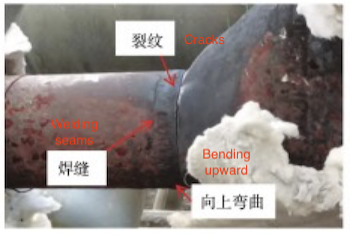
Figure 1 Appearance of cracking positions of SS pipes
2.2 Hardness tests
Use a Leeb hardness tester to conduct hardness tests on the welding seam at the cracked part, the reducing joint, and the base metal of the straight pipe. The hardness value of the welding seam is 164 HB; the hardness value of the reducing joint is 139 HB, and the straight pipe base metal is 131 HB. The hardness value corresponds to its service time.
2.3 The analysis of materials
Use an alloy analyzer to detect the composition of the straight pipe and the joint with different diameters at the cracked part. The alloy composition is consistent with ASME SA -335 P22.
2.4 Metallographic detection
Using an on-site metallographic microscope, conduct metallographic microstructure analysis on the reducing joints and straight pipes near the cracked part. The results show that the metallographic structure of the reducing joint is ferrite, bainite and carbide (Figure 2). According to DL/T 999-2006 "Power Station 2.25Cr-1Mo Steel Spheroidization Rating Standard", the spheroidization grade is rated as 3.5, which is moderate spheroidization. The metallographic structure of the base metal of the straight pipe section is ferrite, bainite and carbide (Figure 3). According to the DL/T 999-2006 standard, the degree of nodularity is rated as 3.0, which is mild spheroidization, and the metallographic structure matches its service time.
Figure 2 Organization of the reducer
3. Historical failures and maintenance summary
On June 25, 2006, cracks also occurred at the same position of the reducer of the high-pressure steam main pipe of the No. 1 boiler. The crack was located on the welding seam fusion line of the small end of the reducer, and cracked from the upper part along the fusion line, as shown in figure 4.
Figure 3 Structure of straight tubes
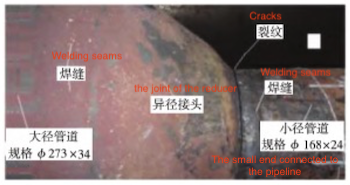
Figure 4 Appearance of cracking of reducers of high-pressure steam main pipes of No. 1 boiler
3.1 Detection
At that time, the repair plan decided to repair the crack, and it was impossible to take samples for analysis, so it was only possible to conduct preliminary inspections through on-site partial inspections. The temperature is finally controlled at 150 to 200°C due to the high temperature, and metallographic testing cannot be performed. Hardness testing at this temperature can only be used as a reference. After hardness testing, the hardness values of the base metal and heat-affected zone of the straight pipe are 149 to 160HB; the hardness value of the welding seam is 219 to 222HB, and that of the base metal and heat-affected zone of the reducing joint is 175 to 191HB. The hardness test is normal.
3.2 Analysis results
According to the preliminary analysis, the reason for the cracking is the stress concentration caused by the discontinuity of the shape of the eccentric reducer and the temperature difference of the pipeline. According to the preliminary analysis, the reason for the cracking is the stress concentration caused by the discontinuity of the shape of the eccentric reducer and the superposition of temperature difference stress of the pipeline, leading to cracking in the weak area of the welding seam.
A super high-pressure steam ( SS ) pipeline is one of the most important pressure pipelines of an ethylene plant, and its long-term stable operation directly affects the output and benefit of an ethylene plant. The 220 kt/a ethylene cracking unit of Dushanzi Petrochemical Company of PetroChina was designed by the British SNAM Company and put into use in August 1995. The ultra-high-pressure steam pipeline was designed, installed and put into use at the same time. The ethylene unit has 7 cracking furnaces in total, and the ultra-high-pressure steam generated by each cracking furnace flows into the main pipe through the globe valve. On April 28, 2022, during the SS grid-connection operation of Furnace No. 4, cracks were found at the welding seam between the high-pressure steam main pipe of the cracking furnace and the tee. Since the device is in operation, the cracked part is repaired by welding after excavation, but it is impossible to take samples of the cracked part for physical and chemical analysis of the fracture. The reason for the cracking can only be determined according to the on-site inspection situation and historical failures.
1. Basic situation of ultra-high pressure steam pipelines
The eccentric reducing joint of the ultra-high pressure steam pipeline is made from A335-P22. The medium of the pipeline is ultra-high pressure steam, the operating temperature 525 ℃, and the operating pressure 12.5MPa. The size of the eccentric reducer is DN150 × DN250 mm; the wall thickness of the side of the small end is 23mm, and the large end 42 mm. On April 28, 2022, a leak was found at the reducer, and the ultra-high pressure is removed from the device immediately. The pressure of the SS system dropped to 1MPa, and the maintenance personnel removed the pipe insulation.
The welding seam at the small end of the pipe reducer is cracked. Judging from the size, opening and appearance of the crack, the crack extends downwards from the upper part along the fusion line. The crack length is about 240 mm. The fracture is flat from the outside. The welding seam was repaired and the cracking furnace was heated up. It is verified that the SS system was put into use in 1995 according to the operating conditions over the years. After inquiry, the number of shutdowns of the device for maintenance and the number of times pressure rise and fall of ultra-high pressure steam pipelines totaled 19 times.
2. Inspection status of ultra-high-pressure steam pipelines
Repairing the cracked parts by welding after excavation cannot be carried out. The complete observation and microscopic analysis of the fracture can only be carried out on-site for visual inspection, only analysis for alloys, on-site metallographic coatings, hardness and other tests can be performed.
2.1 Appearance inspection of reducers
The crack is located on the welding seam’s fusion line of the small end of the reducer of the SS pipeline. From the size and appearance of the crack opening, it is judged that the crack extends downward along the fusion line from the upper part, and the crack length is about 240mm. The short opening is flat viewed from the outside and has obvious characteristics of large stress cracking. There is obvious upward bending deformation at the bottom of the eccentric reducer (figure 1).
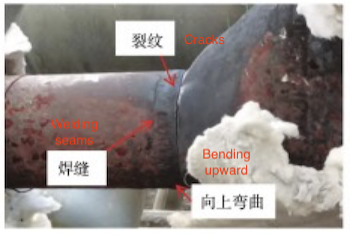
Figure 1 Appearance of cracking positions of SS pipes
2.2 Hardness tests
Use a Leeb hardness tester to conduct hardness tests on the welding seam at the cracked part, the reducing joint, and the base metal of the straight pipe. The hardness value of the welding seam is 164 HB; the hardness value of the reducing joint is 139 HB, and the straight pipe base metal is 131 HB. The hardness value corresponds to its service time.
2.3 The analysis of materials
Use an alloy analyzer to detect the composition of the straight pipe and the joint with different diameters at the cracked part. The alloy composition is consistent with ASME SA -335 P22.
2.4 Metallographic detection
Using an on-site metallographic microscope, conduct metallographic microstructure analysis on the reducing joints and straight pipes near the cracked part. The results show that the metallographic structure of the reducing joint is ferrite, bainite and carbide (Figure 2). According to DL/T 999-2006 "Power Station 2.25Cr-1Mo Steel Spheroidization Rating Standard", the spheroidization grade is rated as 3.5, which is moderate spheroidization. The metallographic structure of the base metal of the straight pipe section is ferrite, bainite and carbide (Figure 3). According to the DL/T 999-2006 standard, the degree of nodularity is rated as 3.0, which is mild spheroidization, and the metallographic structure matches its service time.
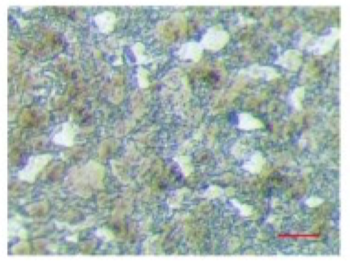
Figure 2 Organization of the reducer
3. Historical failures and maintenance summary
On June 25, 2006, cracks also occurred at the same position of the reducer of the high-pressure steam main pipe of the No. 1 boiler. The crack was located on the welding seam fusion line of the small end of the reducer, and cracked from the upper part along the fusion line, as shown in figure 4.
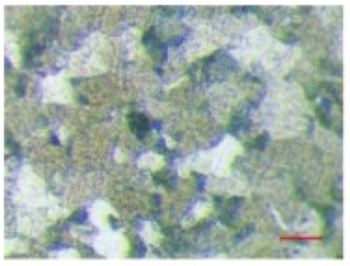
Figure 3 Structure of straight tubes
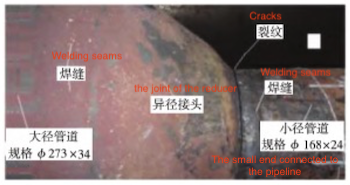
Figure 4 Appearance of cracking of reducers of high-pressure steam main pipes of No. 1 boiler
3.1 Detection
At that time, the repair plan decided to repair the crack, and it was impossible to take samples for analysis, so it was only possible to conduct preliminary inspections through on-site partial inspections. The temperature is finally controlled at 150 to 200°C due to the high temperature, and metallographic testing cannot be performed. Hardness testing at this temperature can only be used as a reference. After hardness testing, the hardness values of the base metal and heat-affected zone of the straight pipe are 149 to 160HB; the hardness value of the welding seam is 219 to 222HB, and that of the base metal and heat-affected zone of the reducing joint is 175 to 191HB. The hardness test is normal.
3.2 Analysis results
According to the preliminary analysis, the reason for the cracking is the stress concentration caused by the discontinuity of the shape of the eccentric reducer and the temperature difference of the pipeline. According to the preliminary analysis, the reason for the cracking is the stress concentration caused by the discontinuity of the shape of the eccentric reducer and the superposition of temperature difference stress of the pipeline, leading to cracking in the weak area of the welding seam.
Post URL: https://www.landeepipefitting.com/cracking-of-welding-seams-of-eccentric-reducers-in-ultra-high-pressure-steam-pipelines.html
Landee is a professional industrial pipe fitting manufacturer and be well accepted by customers all over the world, we has been producing Pipe Fitting for a variety of applications since 1985. welcome to access our website: https://www.landeepipefitting.com.
Previous: Discussion of Cracks of Reducers
Next: Analysis & Preventive Measures for Cracks in Ultra-high Pressure Steam Pipelines
Next: Analysis & Preventive Measures for Cracks in Ultra-high Pressure Steam Pipelines